Simco-ION Static Control Applications


PCB & Electronic Assembly
Printed Circuit Board (PCB) & Electronic Assembly products require protection from the destructive effects of electrostatic discharge (ESD) and particle contamination which can seriously damage sensitive electronic components and assemblies. Simco-ION's extensive line of products from point of use ionizing air guns to benchtop and overhead ionizing blowers and compact ionizers that fit inside of tools are designed to protect production processes such as PCB manufacturing and assembly, surface mount technology, device programming, medical device manufacturing and testing.
Learn more about how Simco-ION can help reduce yield losses and improve product quality in PCB and electronics manufacturing applications.

Flat Panel Display Manufacturing
Stringent contamination control standards for Flat Panel Display (FPD) manufacturing, including in-tool, conveyor and cassette load/unload applications, often require the use of mini-environments and complete room ionization systems to isolate sensitive products from ambient particle contamination during fabrication. Simco-ION's ionizers are ideal for FPD manufacturing processes that require fast discharge times for quick moving glass substrates.
Learn more about how Simco-ION can help reduce yield losses and improve product quality in flat panel display manufacturing applications.
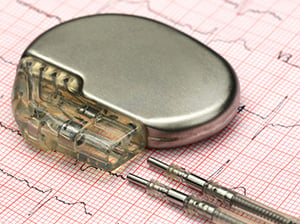
Medical Device Manufacturing
Leveraging our technical expertise in providing ionization solutions to solve particulate contamination - both sub-visible and visible - since 1936 in the high tech industries, we have demonstrated how ionization significantly solves particulate contamination in many global life science companies.
Learn more about how Simco-ION can help reduce yield losses and improve product quality in medical device manufacturing applications.

Front-End Semiconductor Manufacturing
Static charge is generated throughout the semiconductor manufacturing process, caused primarily by the contact and separation of dissimilar materials. Static charge affects productivity and yield in three ways. Static charge electrostatically attracts (ESA) particles from the air causing potential yield loss on wafers and reticles. Electrostatic discharge (ESD) of voltages cause instant or latent defects on reticles, wafers, or packaged chips. Electrostatic discharges can also create electromagnetic interference (EMI), triggering microprocessor lockup and robotic malfunctions that lead to product flow interruptions and costly tool downtime. Our portfolio of static charge control solutions addresses all stages of wafer manufacturing and testing.
Learn more about how Simco-ION can help reduce yield losses and improve product quality in front-end semiconductor manufacturing applications.

Back-End Semiconductor Processing
Typical back-end semiconductor applications where ionization and monitoring solutions improve productivity include the cleanroom area where photolithography, reticle storage and FOUP wash processes. Inside test and assembly tools, ionizers used in combination with ESD event detection and field voltage monitors provide protection against costly ESD damage.
Learn more about how Simco-ION can help reduce yield losses and improve product quality in back-end semiconductor processing applications.